Clientcases
Van Dijck
Extensive automation in fruit and vegetable distribution centre
Based in the north of the province of Limburg, Van Dijck Groenteproducties delivers a wide range of field-grown vegetables to retailers and wholesalers in the Netherlands and across Europe. The organisation’s rapid growth and the construction of its new distribution centre in America called for more automation and control on the work floor. We tailored our soft- and hardware to Van Dijck’s specific processes and wishes.
Realtime insight
Tracking & tracing
In the dynamic fruit and vegetable sector, good traceability is crucial. Growers of fruits and vegetables want to be able to accurately track their products from harvest to delivery. With tracking & tracing, Van Dijck can obtain all relevant information at the press of a button: from the harvest location and date to the products’ weight, time of packaging and destination. The functionalities of the Supply Chain Software also give the company realtime insight into its daily operations, which allows it to e.g. develop reliable prognoses for buyers.
"Today on the land, tomorrow with the customer. In the fruit and vegetable sector, speed and good traceability are paramount." - Quote client
Relevant solutions with this client case
Vanboxtel-WMS
Automatic identification
Support / service
New functionalities for more efficiency
Van Dijck exclusively delivers fresh products, which means its warehouse operates 24/7. Add to that the volume the company processes – during the high season, circa two thousand pallets move in and out of the warehouse and more than sixty fully loaded trucks leave there every single day – and it is easy to see why speed and efficiency are so important. That is where Vanboxtel came in. We developed new functionalities that made it possible to register the reception of pallets much faster and allowed us to eliminate a delaying step from the process. With the new scanning and registration functionality, pallets can now be loaded directly from inventory. The new hand terminals not only let employees work faster and more efficiently, but they have also virtually eliminated the risk of errors.
Want to know more about the used services?
Want to know more about this case and the services that are offered? Feel free to contact us., we will answer your questions as soon as possible.
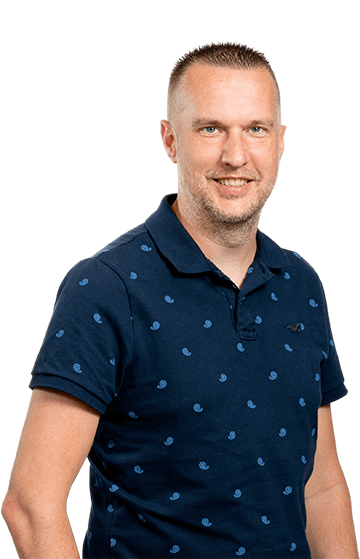